How Sealcoating Can Enhance the Look of Your Driveway
Rochester NY Sealcoating job needs to be done under ideal conditions. It can’t be too hot or too cold and the humidity has to be low.
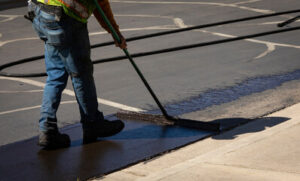
Workers have to wear protective equipment to avoid contact with the coal tar or similar acrylics. The process also takes time and it may be best to split a large project into several days.
Asphalt sealcoating is the process of applying a protective layer to asphalt-based driveways and parking lots. This liquid product fills in small cracks and protects the surface from sun damage. It also replenishes the oils in the asphalt, which helps keep it flexible and prevents brittleness. Asphalt sealants can be made up of different ingredients, but the most common are petroleum products and mineral fillers. The liquid is applied using pressurized spray equipment or self-propelled squeegee machines. A typical application takes 24 to 48 hours before vehicles can be safely re-entered on the lot.
Without seal coating, asphalt is exposed to the elements and the resulting damage can be expensive to repair. In addition, unsealed pavement is susceptible to water damage. This can occur when water seeps through the small cracks and then freezes, expanding the cracked area. Seal coating keeps water out and prevents the damage that it causes.
An unprotected asphalt driveway or parking lot will quickly deteriorate, leaving you with large and costly repairs. Seal coating protects your investment and extends the life of your driveway or parking lot.
The oil in the seal coat seeps down into the asphalt, replenishing the lost oils and lubricating the binder that holds the pavement together. Without these oils, the asphalt becomes brittle and cracks easily. This is why it’s so important to seal your asphalt regularly.
The dark black color of the sealcoat enhances the appearance of your parking lot or driveway and makes it look like new. This is especially important for commercial properties that rely on their curb appeal to attract customers. If your property’s asphalt looks tired and neglected, it may cause a negative impression on customers.
Concrete
Concrete surfaces can be sealed to preserve and enrich their appearance, protect against contaminants and moisture, and make them easier to clean. Concrete sealers are available in a wide range of finishes, from satin to high gloss and are able to withstand a variety of conditions.
The best type of sealant for your decorative or plain concrete depends on what you want it to do, as well as the type of surface. Film forming and penetrating sealers are available, with each providing a unique set of benefits.
Film-forming sealers create a sheen or gloss that enhances the color of the concrete and can provide anti-skid properties. These are typically used on driveways, garage floors, and pool decks. They have a long lifespan and don’t peel or delaminate.
Penetrating sealers are formulated with silanes, siloxanes, and siliconates to penetrate into the concrete and create a chemical barrier. These have a natural matte finish and are recommended for use on concrete patios, sidewalks, and walkways. They can also be used on pavers, brick, sandstone, or other masonry.
A good quality penetrating sealer will last ten years or more, and it can be applied to a new or old surface. It is best to reseal concrete on a regular basis, depending on how much use it gets.
Prior to applying a concrete sealer, the concrete should be thoroughly cleaned and any cracks filled. It’s important to choose a day when temperatures will be moderate so that the sealer doesn’t dry too quickly or too slowly, as this could affect its durability. The work area must be clear of any plants or objects that may get damaged by the chemicals in the sealer, and it’s a good idea to wear protective equipment. Apply the sealer using a roller or sprayer, following the manufacturer’s instructions for coverage and curing times.
Wood
Sealcoating wood makes it easier to apply a stain or other clear finish. It also helps the topcoats not to absorb into the pores of the wood. This is particularly important for soft woods like pine, which can blotch and look dull with a clear coat on it.
A high-quality oil or water-based polyurethane is the best choice for sealing a wood surface. It can be brushed on or sprayed on as needed. It dries quickly and can be sanded or recoated in about an hour. Warmer temperatures accelerate dry time, and colder temperatures prolong it.
When applying the sealant, be sure to work in a well-ventilated area and wear protective gear. Some sealers emit toxic fumes that can be dangerous when inhaled while they are curing.
The most popular sealant for wood is shellac, which comes in a variety of sheens and works well on all types of wood. It’s also a great choice for doors and trim that will be exposed to the elements, because it is resistant to mold growth and mildew. It’s important to sand the wood before applying it and to keep sanding between coats until the surface is smooth.
Another option is a polyurethane varnish, which is available in a range of sheens. It is more durable than shellac and won’t yellow over time. It’s easy to use a brush or rag to apply it, but beware of the toxic fumes while it’s curing. Both oil-based and water-based varnishes release toxic volatile organic compounds into the air while they are curing. If you can’t afford to wait for it to cure completely, a lacquer thinner is available to help remove it.
Brick
Brick is a popular choice for building driveways and parking lots, but it’s susceptible to water damage and staining. It also becomes brittle over time without a seal coat, and it can develop potholes if not properly maintained. Fortunately, seal coating is easy and inexpensive. A good sealant will keep your brick looking like new for years to come.
The type of sealant you choose depends on your climate and the type of brick you have. A sealant with a high concentration of acrylic solids, such as a polyurethane or alkyd enamel, will produce a lustrous finish. This will darken faded pavers, restoring their natural reds and browns while adding a beautiful sheen to the surface. The higher solid content also helps resist abrasion and chemical attack.
Refined coal tar is another popular choice for sealcoating brick surfaces. It’s a thick black liquid that’s derived from the distillation of bituminous coal. This type of sealant is inexpensive and can be used where a petroleum-based product wouldn’t be appropriate, such as on a sidewalk. However, this type of sealant doesn’t provide the best protection against UV rays and does not stand up to salts or petrochemicals.
Before applying any sealant, sweep the surface and remove any dirt or sand particles. Then, use a wire brush to clean the masonry joints and corners where dust and grit often accumulate. If your brick has any cracks, make sure to repair them using a concrete patch mix or mortar.
The ideal time to apply a sealant is when the weather is dry. After application, let the sealant set for 24 hours before using the area again. To ensure the best results, DRYLOK Siloxane 7 Brick & Masonry Penetrating Sealer should be applied following a dry spell of 2 or 3 days.
Metal
Having your metal driveway, curbs and other surfaces regularly sealcoated will extend the life of them. In addition, it will prevent corrosion and save you money in the long run because you won’t have to pay for expensive repairs or replacements.
First, the area to be worked on must be cleaned thoroughly. A power washer and/or high powered blowers are used to remove any dirt, debris or other materials that would interfere with the sealcoating process. Once this is done, the work can begin. A professional service company will clearly barricade off the area with cones and/or caution tape to keep pedestrians and vehicular traffic away from the work zone.
Once the work is underway, the crew will start by mixing the sealcoat. Each barrel of sealcoat has a special lid with a hole that can be popped open to allow for easy mixing. Once the sealcoat is mixed properly, it can be poured on the surface of the asphalt.
When pouring, it is important to spread the coat evenly. If not, the final result will be uneven and the appearance will look bad. The sand must also be properly calibrated to ensure the desired texture and traction. This can be achieved by using a specific sand gradation, per manufacturer specifications.
Then, any oil spots or oxidized areas must be treated with an appropriate oil spot primer or a tack coat. Finally, the surface should be fully cured before it is sealed again. Failure to do this will cause the new coat to crack and peel. It is also important to remember that it’s a good idea to use long sleeved gloves, pants and impervious boots when working with sealcoat.